LEAN to Improve Series - 2 weeks of extra production a year from just 20 minutes a day
How many times have you said to yourself, “If only we could fill that order.”? Have you caught yourself saying, “If only there were more hours in the day.”? If you are like most manufacturing companies, you say this almost every day. There never seems to be enough time in the day to produce what you need. There is hope though, you can get an extra two weeks of production per year in just 20 minutes a day. I know 20 minutes a day doesn't sound like much, but it adds up.
Where do I find those 20 minutes a day?
It sounds like a daunting task to find 20 minutes of production per day. However, it is a lot easier than you think. Even the leanest of manufacturing facilities has waste, or non-value-added-work. You just need to know how to identify it. Lean practitioners are specifically trained to identify waste but it's not a hard skill for you to learn. Most people can do it naturally if they first know what they're looking for. So, let's talk about what is waste.
In Lean practices, there are eight categories for waste, and they are:
Transportation: I know what you're thinking. Transportation is not a waste. You have to get things from one location to another. However, there is such a thing as excess transportation. How often do you move materials in and out because you oversupplied a single machine? Is production set up in a way where product flow from one location to the next is in the shortest path?
Inventory: How can inventory be a problem? Let me ask you these questions - Do you have items that sit on the shelf that you do not sell anymore? Do you have machines that don't operate but take up space? Do you hold a perishable item and have to throw away some of the stocked material because of the expiration dates? When we talk about the waste of inventory, we're talking about situations that cost money but produce no item.
Motion: This is probably one of the most common wastes that I see. I think we can all agree that the goal of any facility is to have employees produce items for as much of the day as possible. Every minute that they must be away from their workstation looking for materials or tools is a waste of time, and time is money. Unlike transportation where we were looking at specific movement of the materials through the facility, motion focuses on the individual.
Waiting: This may be the most obvious to identify for new practitioners. Anytime someone is waiting for job assignments, responses from other departments, or delivery of components from another station, production is being eroded away. Whether it's minutes or hours, it's time that should be spent producing goods or delivering services.
Over-Processing: Overprocessing can easily be identified when you look at the sales figures for the product or service. Do you have items that you've made changes to that do not sell anymore? Have you asked the client why they don't want it? Over processing means adding more to the product than the client is willing to pay for.
Overproduction: While holding more than you need is waste of inventory, making more in a process than you need is waste of overproduction. How balanced is your production process? Are there locations where WIP (Work in Process) builds up to uncontrollable levels? Did you make so much more than the client could consume that you have leftovers? WIP is not a bad thing. It just should be minimized to an amount that is easily controlled and never an excess of what the client would consume.
Defects: I think we're all aware that defects are a waste. Parts that don't pass inspection are commonplace in most smaller industries. Besides the cost of materials and wages, defects risk the cost of the company’s reputation if they get into the marketplace. Too often I see companies fear this risk of reputation so much, they place an inspection station at every workstation throughout the process. What this tells me is that the root cause of the actual problem has never been identified. In another article will discuss finding root cause problems so that you can develop solutions and not use band-aids.
Skills: You're probably saying to yourself, how do I waste skills? You waste skills when you use an individual with a specific skill set to perform another task or menial tasks. When someone does something that requires limited skills, when they are highly skilled in something else, it is a waste of their talent as well as the money you are paying them.
Now I know, you're not reading this article to learn what waste is. You’re reading this article to find some quick wins and save time. However, you need to know what waste is so you can identify it. As you recognize waste in your manufacturing operation, you can reduce or remove it, saving time and money.
Let's talk about a few quick wins that you can find with some easy observation.
Take 15 minutes a day and observe the areas that are under your control. Are employees looking for <Insert object necessary to perform their job>? If they are, stop them, and ask them what they're looking for. Then you can reduce the waste of motion and create a solution that will prevent it from happening again. The concept is easy. The implementation can often be difficult. Consider this, if every employee spends even 5 minutes every day looking for something they need to do their job and you can stop that from happening, that adds up to almost an additional 20 hours of production a year per employee. Take a moment and think about that. You could save 20 hours of overtime by saving 5 minutes a day per employee. I don't know about you, but to me that's a lot of money.
Where else can you find more time? How often does your shift start on time? It's a lot easier said than done, too. How do you get people to actually start at the beginning of their shift? This takes effort from supervisors, leads, managers, directors, owners, etc. Everyone must be involved with setting the correct expectations. This begins by putting the expectation into the company’s policies and employee handbook. Once everyone is aware of the standard they will be held to, the next step is to begin the most difficult part of the process, getting them to follow the policies. One way to do this is to create a start of the shift meeting to assign work to individuals. I know what you're saying, this takes up time, but if it takes five minutes and you are wasting 20 minutes each day with employees looking around having conversations or just getting their first cup of coffee, you’ve saved 15 minutes. 15 minutes is an additional 60 hours of production a year per employee. This same process could be applied to lunches and breaks but instead of a meeting you could use a bell, or have supervisors check on the employees to make sure they're not abusing the times.
No matter what you do to reduce the waste in your operation, you will find it all adds up to saved time and/or money. Whether it's one of the wastes in this article, or a mechanical issue which we will discuss in a future article, minutes will add up to hours. I'm going to leave you with this one piece of advice, go and observe. Get out on the floor and see what is going on. You should always inspect what you expect. Take a walk at the beginning of the shift to make sure everyone is working. Do this same check at breaks and lunches, as well as the end of the day.
Look for an article and a webinar about 5S. How an organized workspace increases productivity the week on April 25th.
Check out our EVENTS page for LEAN to Improve Series webinars and trainings for additional Continuous Improvement expert insight and actionable recommendations.
KMS's Continuous Improvement expert is here to answer your questions or come by your facility to provide a Continuous Improvement assessment. CONTACT us to get your questions answered or REQUEST an assessment today!
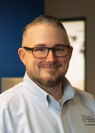